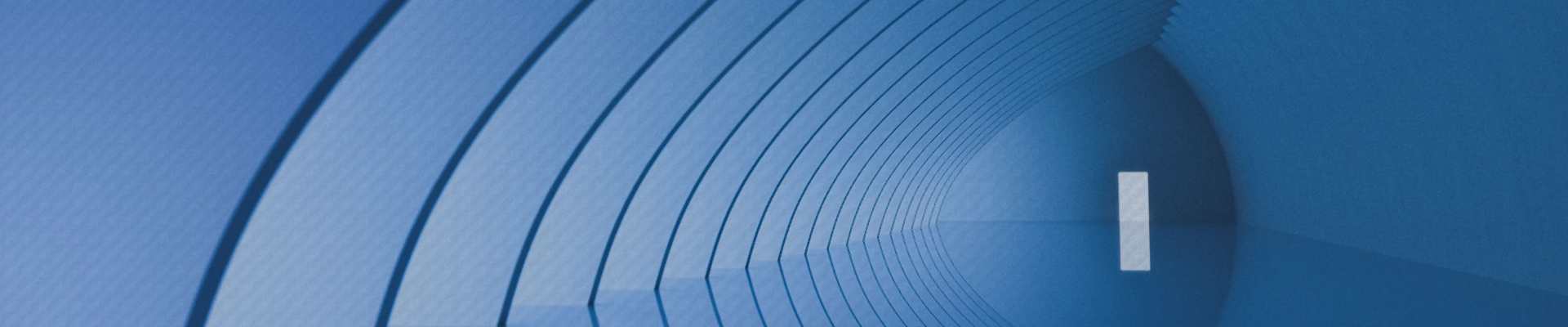
混凝土,作为现代建筑中不可或缺且至关重要的材料之一,其质量直接关乎建筑物的结构安全性与长期耐久性。然而,在实际施工进程中,混凝土强度不达标的问题却屡见不鲜,这无疑对工程质量构成了严峻挑战,更可能潜藏着对人们生命财产安全造成威胁的风险。那么,究竟是何原因导致了混凝土强度不足这一棘手问题的出现呢?本文将对此展开深入剖析,从原材料的质量控制、配合比的精准设定、施工工艺的严格执行,以及试块管理的规范操作等四大核心方面,细致阐述引发混凝土强度不足的具体缘由,以期为行业同仁提供有益的参考与启示。
(1)水泥质量不佳导致的隐患
① 水泥实际活性(强度)低
水泥作为混凝土的核心组成部分,其实际活性(强度)对混凝土的整体性能起着决定性的作用。然而,在实际工程中,我们常常会遇到水泥实际活性低下的问题,这主要由两种情况导致。
首先,水泥出厂质量不佳是引发这一问题的常见原因。在水泥生产过程中,若原材料选择不当、配比不合理或生产工艺存在缺陷,都可能导致水泥出厂时质量就存在瑕疵。而当这样的水泥被应用到实际工程中时,若在水泥28天强度试验结果未出之前,就基于估计的水泥强度等级来配置混凝土,那么当28天实测水泥强度低于原估计值时,就会造成混凝土强度不足,进而影响整个工程的质量和安全。
其次,水泥的保管条件和储存时间也是影响水泥实际活性的重要因素。若水泥在储存过程中保管条件不佳,如受潮、受高温或受其他化学物质的影响,都可能导致水泥结块、活性降低。同样,若水泥储存时间过长,也会因水泥中的化学成分发生变化而导致活性降低。这些情况都会使水泥在混凝土中的作用减弱,从而影响混凝土的强度和耐久性。
② 水泥安定性不达标
水泥的安定性是确保混凝土质量稳定的关键因素之一。然而,当水泥中的石膏掺量过多时,会与水泥水化后的产物——水化铝酸钙发生反应,生成水化铝硫酸钙。这种反应会导致体积膨胀,对水泥结构造成潜在的破坏。
更为严重的是,如果这些体积变化在混凝土硬化后产生,那么它们将直接破坏已经形成的水泥结构。这种破坏往往表现为混凝土的开裂,不仅影响美观,更降低了混凝土的强度和耐久性。
特别需要警惕的是,有些安定性不合格的水泥所配制的混凝土,在表面看似并无明显裂缝的情况下,其强度却可能极度低下。这种情况下的混凝土,如同隐藏的定时炸弹,随时可能对工程的安全构成严重威胁。
(2)集料(砂、石)质量不良的影响
① 石子强度低导致的混凝土强度下降
在混凝土的构成中,石子作为骨料起着支撑和增强作用。然而,在实际工程中,我们有时会遇到石子强度低的问题,这对混凝土的实际强度产生了显著的影响。
在一些混凝土试块的试压过程中,我们可以观察到不少石子被压碎的现象。这一观察结果直接表明,所使用的石子强度低于混凝土的强度要求。当石子无法承受混凝土所受的压力时,它们会发生破碎,从而导致混凝土的整体结构受到破坏,实际强度下降。
② 石子体积稳定性差对混凝土强度的破坏
在混凝土的配制过程中,石子的选择至关重要,不仅因为其强度直接影响混凝土的整体性能,其体积稳定性也是一个不可忽视的因素。特别是由多孔燧石、页岩、带有膨胀黏土的石灰岩等制成的碎石,在特定的环境条件下,其体积稳定性往往表现不佳。
这些碎石在干湿交替或冻融循环的作用下,容易发生体积变化,表现出明显的体积不稳定性。这种不稳定性会导致混凝土内部结构的破坏,进而影响混凝土的整体强度。具体来说,当这些碎石在混凝土中受到环境因素的影响而发生体积膨胀或收缩时,它们会与周围的水泥砂浆产生相对位移,导致混凝土内部出现微裂缝。这些微裂缝会逐渐扩展并相互连接,最终形成宏观的裂缝,使混凝土的强度显著降低。
③ 石子形状与表面状态对混凝土强度的影响
石子作为混凝土中的关键组成部分,其形状与表面状态对混凝土的性能有着至关重要的影响。特别是针片状石子含量高时,会显著影响混凝土的强度。这类石子的形状不规则,表面平滑,与水泥的粘结力较弱,因此在混凝土中难以形成有效的应力传递,导致混凝土整体强度下降。
相反,具有粗糙和多孔表面的石子,因其与水泥能够产生更好的粘结效果,从而对混凝土强度产生有利的影响。这种良好的结合使得混凝土在受力时,石子与水泥基体之间能够更好地共同承担应力,特别是提高混凝土的抗弯和抗拉强度。
实际上,在水泥和水灰比相同的条件下,碎石混凝土通常比卵石混凝土的强度高约10%左右。这一现象正是石子形状与表面状态对混凝土强度影响的直观体现。碎石的不规则形状和粗糙表面增加了其与水泥的接触面积,提高了粘结力,从而使得碎石混凝土具有更高的强度。
④ 集料中有机杂质含量高对混凝土的不利影响
集料作为混凝土的重要组成部分,其质量对混凝土的性能有着至关重要的影响。特别是当集料(尤其是砂)中含有较高的有机杂质时,如腐烂的动植物等,这些杂质中的鞣酸及其衍生物会对水泥的水化过程产生不利影响,进而导致混凝土强度的显著下降。
具体来说,这些有机杂质在混凝土中会与水泥发生化学反应,干扰水泥的正常水化过程。这种干扰会破坏水泥石的结构,使其变得疏松多孔,从而降低混凝土的强度和耐久性。此外,这些有机杂质还可能成为混凝土中的薄弱点,为裂缝和破损提供发展的温床。
⑤ 黏土、粉尘含量高对混凝土强度的削弱作用
黏土和粉尘作为混凝土中可能存在的杂质,其含量高时会对混凝土强度产生显著的负面影响。这种影响主要体现在以下三个方面:
首先,这些细小的黏土和粉尘微粒往往会包裹在集料的表面,形成一层隔离层。这层隔离层会阻碍集料与水泥之间的有效粘结,从而降低混凝土的整体强度。因为集料与水泥之间的粘结力是混凝土强度的重要组成部分,任何阻碍这种粘结的因素都会导致强度的下降。
其次,黏土和粉尘的高含量还会增加集料的表面积。集料表面积的增加意味着需要更多的水泥浆来包裹和润滑这些集料,以达到所需的和易性。然而,这也会导致用水量的增加,进而降低混凝土的实际强度。因为过多的水分会削弱水泥浆的稠度,使得混凝土在硬化过程中更容易出现裂缝和孔隙。
最后,黏土颗粒的体积不稳定性也是一个不容忽视的问题。黏土具有干缩湿胀的特性,这意味着在混凝土硬化过程中,黏土颗粒的体积可能会发生变化。这种体积变化会对混凝土的内部结构造成破坏,导致混凝土强度的降低。具体来说,黏土颗粒的膨胀可能会产生微裂缝,而收缩则可能导致混凝土内部的孔隙率增加。
⑥ 三氧化硫含量高对混凝土的破坏作用
集料中若含有硫铁矿(FeS2)或生石膏(CaSO4·2H2O)等硫化物或硫酸盐,并且这些成分的含量以三氧化硫计较高时,例如超过1%,就可能对混凝土的性能构成潜在威胁。这是因为这些硫化物或硫酸盐有可能与水泥的水化物发生化学反应,生成硫铝酸钙。
硫铝酸钙的生成往往伴随着体积的膨胀,这种膨胀效应在混凝土硬化过程中尤为显著。它可能导致硬化的混凝土内部产生裂缝,这些裂缝不仅破坏了混凝土的整体性,还大大降低了其强度。此外,硫铝酸钙的生成还可能改变混凝土内部的微观结构,进一步削弱其力学性能。
⑦ 砂中云母含量高对混凝土物理力学性能的不利影响
云母,作为一种常见的矿物成分,在砂中的含量若过高,将会对混凝土的物理力学性能构成不小的挑战。这主要归因于云母表面的光滑特性,导致其与水泥石的粘结性能极差。在混凝土拌合过程中,云母颗粒往往难以与水泥浆体形成有效的粘结,从而在混凝土内部形成潜在的薄弱区域。
更为严重的是,云母极易沿其节理裂开。这意味着在混凝土受力时,云母颗粒可能成为裂缝发展的起点,进而降低混凝土的强度和耐久性。此外,云母颗粒还可能干扰混凝土内部的应力传递,导致混凝土在受力时表现出不均匀的应力分布,进一步削弱其整体性能。
(3)拌合水质量对混凝土强度的影响
拌制混凝土时,拌合水的质量是至关重要的。然而,如果使用了有机杂质含量较高的沼泽水、含有腐殖酸或其它酸、盐(特别是硫酸盐)的污水和工业废水,那么这些不合格的拌合水将成为混凝土性能的隐形杀手。
这些有害物质在混凝土中会与水泥发生复杂的化学反应,干扰水泥的正常水化过程,破坏水泥石的结构,使其变得疏松多孔。这不仅会导致混凝土的强度大幅下降,还会影响其耐久性,使得混凝土更容易受到外界环境的侵蚀和破坏。
具体来说,有机杂质可能会阻碍水泥颗粒之间的粘结,形成薄弱区域;腐殖酸和其他酸可能会与水泥中的氢氧化钙反应,生成无胶凝能力的物质,进一步削弱混凝土的强度;而硫酸盐则可能与水泥中的铝酸三钙反应,生成硫铝酸钙,导致体积膨胀和裂缝的产生。
(4)外加剂质量差对混凝土强度的破坏
在混凝土的生产过程中,外加剂作为改善混凝土性能的关键材料,其质量的好坏直接影响着混凝土的整体品质。然而,目前市场上存在一些小厂生产的外加剂质量不合格的现象,这给混凝土的性能带来了潜在的威胁。
这些质量不合格的外加剂,往往由于生产工艺落后、原材料质量差、配方不合理等原因,导致其在混凝土中无法发挥应有的效果。更为严重的是,这些劣质外加剂有时还会对混凝土造成负面影响,如导致混凝土强度不足、凝结时间延长甚至不凝结等,给工程带来严重的质量和安全隐患。
混凝土配合比,作为决定其强度的关键因素之一,其重要性不容忽视。在配合比中,水灰比的大小如同天平的秤砣,直接左右着混凝土的强度。而用水量、砂率、浆集比等因素,则如同天平的游码,微妙地调整着混凝土的各种性能。一旦这些因素的配合出现偏差,就可能引发强度不足的事故,给工程带来不可估量的损失。在工程施工的实践中,配合比不当的问题往往表现在以下几个方面。
(1)随意套用配合比
混凝土配合比,这一决定混凝土强度的关键要素,其制定需充分考虑工程特点、施工条件以及原材料的实际状况。通常,工地会向实验室提出申请,经过试配后确定最适宜的配合比。然而,在实际操作中,不少工地却忽视了这一科学流程,仅仅依据混凝土强度等级的指标,便随意套用配合比。
这种不负责任的做法,无疑为工程埋下了巨大的隐患。由于未充分考虑特定条件,随意套用的配合比往往无法满足工程实际需求,进而导致混凝土强度不足,引发一系列质量事故。这不仅影响了工程的整体质量,还可能对人们的生命财产安全构成严重威胁。
(2)用水量加大
在混凝土制备过程中,用水量的控制是至关重要的。然而,在实际施工中,我们常常会遇到用水量加大的情况,这主要是由于搅拌设备上加水装置的计量不准确、未扣除砂石中的含水量,甚至在浇灌地点任意加水等原因造成的。
这种用水量的随意增加,对混凝土的性能产生了极大的影响。它使得混凝土的水灰比和坍落度增大,进而导致了混凝土强度的降低。我们知道,水灰比是决定混凝土强度的关键因素之一,水灰比的增大意味着混凝土中水的含量相对增多,而水泥的含量相对减少,这必然会导致混凝土强度的下降。同时,坍落度的增大也会使得混凝土在浇灌时更易于流动,但却降低了其密实性和强度。
(3)水泥用量不足
在混凝土制备过程中,水泥作为关键的胶凝材料,其用量的准确性对于保证混凝土的强度至关重要。然而,在实际施工中,我们常常会遇到水泥用量不足的情况。这除了搅拌前计量设备可能存在的不准确问题外,包装水泥的重量不足也是一个屡有发生的问题。
当混凝土中的水泥用量不足时,其胶凝作用将受到严重影响,导致混凝土的整体强度偏低。这种强度不足的情况不仅会影响混凝土的承载能力和耐久性,还可能对工程结构的安全性构成潜在威胁。
(4)砂、石计量不准
砂、石的计量不准也是导致混凝土强度不足的一个常见原因。这可能是由于计量工具陈旧或维修管理不好、精度不合格等原因造成的。当砂、石的计量不准时,就会导致混凝土中各组分的比例失衡,从而影响其强度。
(5)外加剂用错
在混凝土制备过程中,外加剂的使用扮演着至关重要的角色。它们能够显著改善混凝土的工作性能,提高施工效率,并赋予混凝土特定的性能,如早强、缓凝、减水等。然而,在实际施工中,外加剂使用不当的问题却时有发生,这主要体现在两个方面。
首先,品种用错是一个常见的问题。在未充分了解外加剂的性能之前,盲目地选择并掺加外加剂,往往会导致混凝土无法达到预期的强度。例如,将本应用于缓凝的外加剂错误地用于需要早强的混凝土中,或者将减水剂误用为增强剂,都会严重破坏混凝土的性能,给工程带来潜在的质量隐患。
其次,掺量不准也是外加剂使用不当的一个重要表现。外加剂的掺量需要严格控制,以确保其在混凝土中发挥最佳效果。然而,在实际施工中,由于计量设备的不准确、操作人员的疏忽或经验不足等原因,外加剂的掺量往往难以准确控制。这不仅会影响外加剂的效果,还可能对混凝土的性能产生负面影响,如强度下降、工作性能变差等。
(6)碱——集料反应
在混凝土制备与施工过程中,碱-集料反应是一个不容忽视的问题。当混凝土中的总含碱量较高,并且使用了含有碳酸盐或活性氧化硅成分的粗集料时,就可能引发这一反应。这些粗集料可能来源于蛋白石、玉髓、黑曜石、沸石、多孔燧石、流纹岩、安山岩、凝灰岩等岩石的制成品。
碱-集料反应的过程是这样的:碱性氧化物在水解后形成氢氧化钠与氢氧化钾,这两种化学物质会与活性集料发生化学反应,生成一种具有吸水性和膨胀性的混凝凝胶。这种凝胶的不断生成和吸水膨胀,会对混凝土造成严重的破坏,导致开裂或强度下降。
日本的相关资料表明,在其他条件相同的情况下,发生碱-集料反应的混凝土强度可能仅为正常值的60%左右。这一数据充分说明了碱-集料反应对混凝土性能的巨大影响。
混凝土施工工艺的每一个环节都至关重要,任何细微的差错都可能对混凝土的最终强度产生显著影响。以下是对该环节中存在的一些核心问题的深入探讨:
(1)混凝土拌制不佳
在混凝土拌制过程中,若加料顺序不当,搅拌时间不充分,将直接导致拌合物均匀性受损,进而影响其整体强度。具体来说,若将骨料、水泥、水等原材料的加入顺序颠倒,或者搅拌时间过短,未能使各组分充分混合均匀,就会使得混凝土拌合物中出现局部材料聚集或分散不均的情况。这种不均匀性会导致混凝土在硬化过程中产生内部应力集中,从而降低其抗压、抗拉等力学性能,严重影响混凝土的使用效果和耐久性。
(2)运输条件差
在混凝土的运输过程中,若遇到条件不佳的情况,如运输工具选择不当、运输路线颠簸或运输时间过长等,都可能对混凝土的质量产生不良影响。特别是在运输过程中发现混凝土出现离析现象时,若未能及时采取有效措施进行纠正,如重新搅拌等,将导致混凝土的均匀性和密实性受损,进而影响其整体强度。
此外,运输工具的漏浆问题也是不容忽视的。若运输工具存在密封性不佳或磨损严重等问题,将导致混凝土在运输过程中出现浆体流失,不仅会造成材料的浪费,还会使混凝土的配合比发生改变,进而影响其强度和耐久性。
(3)浇筑方法不当
混凝土的浇筑方法是影响其强度的关键因素之一。然而,在实际施工中,常常由于操作不当或疏忽,导致浇筑方法失当,进而给混凝土的强度带来隐患。
例如,当混凝土在浇筑时已经初凝,其流动性和可塑性将大大降低,这使得混凝土难以充分填充模板,导致浇筑不密实,进而影响其强度。此外,如果混凝土在浇筑前已经发生离析,即水泥浆与骨料分离,那么浇筑后的混凝土将出现不均匀现象,其整体强度也会受到严重影响。
(4)模板严重漏浆
在混凝土施工过程中,模板的选用和安装质量对混凝土成型后的质量有着至关重要的影响。然而,在某工程中,由于钢模严重变形,板缝宽度达到了惊人的5~10mm,导致了严重的漏浆问题。这不仅破坏了混凝土的均匀性和密实性,还使得大量的水泥浆流失,严重影响了混凝土的强度和耐久性。
实测数据显示,该工程中的混凝土在28天后的强度仅达到了设计值的一半,这一结果无疑令人震惊。这也再次提醒我们,模板的选用和安装必须严格控制,确保模板的平整度和密封性,以避免类似的质量问题发生。否则,不仅会影响混凝土的强度,还可能对整个工程的安全性和耐久性造成严重的威胁。
(5)成型振捣不密实
在混凝土成型过程中,振捣工艺的执行情况对混凝土的密实性和强度具有决定性影响。然而,在实际施工中,往往由于振捣不实或模板漏浆等问题,导致混凝土入模后的空隙率高达10%~20%,这不仅破坏了混凝土的均匀性和密实性,还为其强度埋下了严重隐患。
振捣不实会导致混凝土内部出现大量空洞和气泡,这些缺陷会显著降低混凝土的抗压强度和耐久性。同时,模板漏浆问题也会进一步加剧混凝土的空隙率,使水泥浆流失,导致混凝土的整体结构变得疏松,强度大幅下降。
(6)养护制度不良
混凝土的养护制度是确保其强度发展的关键环节。然而,在实际施工中,由于温度、湿度控制不当,常常导致养护制度执行不力,进而对混凝土的强度产生不良影响。
具体来说,如果混凝土在养护过程中温度过低或湿度不足,将导致其早期缺水干燥,这不仅会延缓水泥的水化反应,还会使混凝土内部产生收缩裂缝,从而降低其整体强度。同样,如果混凝土在早期受到冻害,其内部水分会结冰膨胀,对混凝土结构造成破坏,进一步导致其强度下降。
在混凝土试块的管理过程中,存在诸多疏漏,严重影响了试验结果的准确性,进而可能对工程质量造成误判。以下是对试块管理不善的具体剖析:
(1)试块未经标准养护
至今,仍有一部分工地和施工试验检测人员对混凝土试块的标准养护条件缺乏足够的了解,未能意识到试块应当在温度为(20±2)℃、相对湿度95%以上的严格条件下进行养护。这一标准的制定,旨在确保试块能够在最佳的环境中硬化,从而准确反映混凝土的实际强度。然而,由于认知的缺失或管理的疏忽,这些试块往往被置于施工现场的同条件下进行养护,而这样的环境往往难以保证稳定的温度和湿度,更无法提及避免物理损害。
在这种非标准的养护条件下,试块可能会经历剧烈的温度波动、湿度不足,甚至遭受意外的撞砸。这些因素都会严重干扰混凝土的正常硬化过程,导致试块内部结构的缺陷和强度的显著降低。因此,当这些试块被用于评估混凝土的强度时,所得的结果往往偏低,无法真实反映混凝土的实际性能。这不仅可能对工程质量造成误判,还可能对结构的安全性构成潜在威胁。
(2)试模管理差
试模作为制作混凝土试块的重要工具,其管理状况直接关系到试块的质量。然而,在实际施工过程中,试模的管理往往存在诸多疏漏。当试模出现变形时,若不及时进行修理或更换,将导致试块在制作过程中产生不规则的变形。这种变形不仅破坏了试块的外观完整性,更严重影响了其内部结构的均匀性和密实性。
进一步来说,由于试模管理不善,还可能制作出缺边、缺角的试块。这些试块在受力时,由于形状的不规则,会导致应力分布不均,从而降低其抗压强度等力学性能。这样的试块用于混凝土强度的评估,无疑会导致试验结果的偏差,甚至可能对工程质量产生误判。
(3)不按规定制作试块
在混凝土试块的制作过程中,必须严格遵守相关规范和标准,以确保试块的质量能够真实反映混凝土的实际性能。然而,在实际施工中,不按规定制作试块的现象时有发生,这给试验结果的准确性带来了严重影响。
具体来说,一些常见的违规操作包括试模尺寸和石料粒径不相适应、试块中石子过少以及试块没有用相应的机具振实等。当试模尺寸与石料粒径不匹配时,会导致试块内部石子分布不均,进而影响其力学性能。而试块中石子过少,则会使试块的密实度降低,同样会影响其强度。此外,如果试块没有用相应的机具振实,其内部将存在大量空洞和气泡,这也会显著降低试块的强度。
综上所述,导致混凝土强度不足的原因是多方面的,包括原材料质量、配合比不当、施工工艺存在问题以及试块管理不善等。为了避免这些问题的发生,我们必须从源头抓起,严格控制原材料的质量;同时,还要根据工程的实际情况和原材料的性质,制定合理的配合比;在施工过程中,要严格遵守施工工艺的要求;最后,还要加强对试块的管理和检测工作。只有这样,才能确保混凝土的质量和安全性能达到预期的要求。
内容来源:砼界
免责声明:本文涉及的部分文案、图片、视频摘自于互联网,目的在于分享更多信息,本站不对其准确性负责。部分内容、图片系网络转载,版权归原作者所有,部分内容因转载众多,无法确认原作者,如有问题,请联系删除。