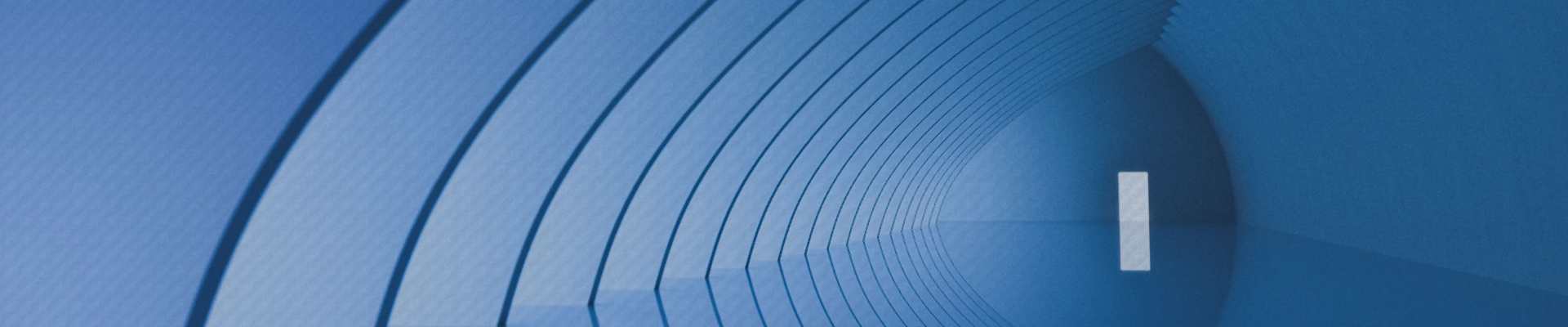
混凝土作为现代建筑中不可或缺的材料,其性能的稳定性和耐久性直接关系到建筑结构的安全与使用寿命。然而,在实际施工过程中,混凝土开裂是一个常见且不容忽视的问题。本文将深入探讨导致混凝土开裂的十大原因,旨在提高施工人员的质量意识,减少裂缝的产生,确保工程质量。
1、施工过程中擅自改变水灰比
在泵送混凝土施工的过程中,一个不容忽视的问题便是施工人员擅自调整水灰比的现象。为了追求施工过程中的便利性,或是出于其他种种考量,部分施工人员往往会选择擅自向混凝土中加水,以此来提高其流动性。然而,这种看似微不足道的行为,实则隐藏着巨大的安全隐患。
水灰比作为混凝土配合比中的关键参数,其精确性直接关系到混凝土的最终性能。当施工人员随意调整水灰比,特别是增加水分含量时,会导致混凝土在硬化过程中产生更大的收缩量。这种收缩不仅会在结构表面形成错综复杂的网状裂缝,还可能产生长短不一、形态各异的不规则裂缝。
这些裂缝的存在,不仅严重损害了建筑的美观性,更对混凝土的力学性能造成了不可忽视的削弱。它们如同隐藏在建筑结构中的“定时炸弹”,为建筑的长期稳定性和安全性埋下了巨大的隐患。
2、混凝土运输搅拌时间过长
在混凝土的施工流程中,搅拌与运输无疑是两个至关重要的环节,它们直接关乎到混凝土材料的最终品质。然而,在实际操作中,若搅拌与运输的时间过长,便会对混凝土的性能产生不利影响,尤其是会导致其中的水分大量蒸发。
当混凝土在搅拌和运输过程中长时间暴露于空气中时,其内部的水分会逐渐蒸发,从而使得混凝土的塌落度显著降低。塌落度的变化会直接影响到混凝土的流动性和可塑性,进而在浇筑和成型过程中产生不规则的收缩裂缝。这些裂缝在初期可能并不明显,甚至可能被忽视,但随着时间的推移和外部环境的影响,它们会逐渐扩大,对混凝土结构的安全性和稳定性构成严重威胁。
3、模板作业不规范
模板作业在混凝土施工中扮演着举足轻重的角色,它是确保混凝土成型精确度和整体质量的关键所在。模板的刚度和稳定性,作为衡量其性能的重要指标,对混凝土的最终品质有着深远的影响。
当模板的刚度不足时,其抵抗变形的能力便会大打折扣。在浇筑混凝土的过程中,由于混凝土的侧向压力作用,模板很容易发生形变,这种形变会直截了当地反映在混凝土上,导致混凝土表面产生与模板变形相吻合的裂缝。这些裂缝不仅损害了混凝土的美观性,更可能对其结构性能造成不利影响。
除了模板刚度不足外,拆模过早也是引发裂缝的一个重要因素。在混凝土强度尚未达到设计要求的情况下,过早地拆除模板,会使得混凝土构件在自重或施工荷载的作用下产生裂缝。这种裂缝往往难以预测和控制,对施工质量构成严重威胁。
此外,模板支架的压实度和刚度也是影响混凝土质量的关键因素。如果支架压实不足或刚度不够,浇筑混凝土后,支架可能会发生不均匀下沉,导致混凝土出现裂缝。同时,模板在浇筑前的淋水工作也不容忽视。如果淋水不足,模板会过分干燥,从而在浇筑后吸收大量水分,导致混凝土收缩,进而产生塑性收缩裂缝。
4、施工工艺不合理
施工工艺的严谨性与施工现场的高效管理,是确保混凝土质量不可或缺的两大基石。在实际施工过程中,若施工工艺缺乏合理性,或现场管理陷入混乱,势必会对混凝土的质量造成严重影响。具体来说,施工现场若不加节制地堆放施工机具与材料,不仅会占用宝贵的施工空间,还可能因堆放不当导致机具、材料对混凝土结构产生额外的压力或冲击,从而增加裂缝产生的风险。此外,对于预制结构而言,若施工人员对其受力特点了解不足,便可能在进行翻身、起吊、运输和安装等作业时采取不当操作,这些操作同样会对混凝土结构造成损害,引发裂缝。
更为严重的是,部分施工人员可能不按设计图纸进行施工,或擅自更改结构施工顺序,甚至改变结构受力模式。这些行为无疑是对施工规范的严重违背,它们将极大地削弱混凝土结构的稳定性和安全性,导致裂缝等质量问题的频繁出现。
同时,施工现场的人员管理也至关重要。若施工人员随意乱踩已绑扎的上层钢筋,不仅会破坏钢筋的排列顺序,还可能使承受负弯矩的受力筋保护层加厚。这种加厚现象将导致构件的有效高度减小,进而降低其承载力,最终在混凝土结构中形成与受力钢筋垂直方向的裂缝。
5、施工速度过快
施工速度的快慢,直接关系到混凝土结构的成型质量与长期性能,而过快的施工速度往往是诱发混凝土开裂的一个重要因素。当浇筑混凝土的过程过于迅速时,混凝土的流动性可能会受到显著影响,变得不再那么顺畅。这种情况下,混凝土在硬化前的沉降时间不足,导致其在硬化后沉降量过大,进而引发一系列问题。
特别是在浇筑后的数小时内,过快的施工速度容易导致钢筋上方、墙与板交接处、梁与柱连接点等关键部位出现沉降收缩裂缝。这些裂缝的产生,不仅破坏了混凝土结构的整体性,使得结构的外观和质量受到损害,更可能进一步影响到结构的承载力,对建筑物的安全性和稳定性构成潜在威胁。
6、没有正确振捣
振捣作业在混凝土施工中占据着举足轻重的地位,它是确保混凝土密实度与均匀性的关键环节。然而,在实际操作中,若振捣不密实或不均匀,便会在混凝土内部遗留下蜂窝、麻面、空洞等一系列缺陷。这些看似微不足道的缺陷,实则成为了钢筋锈蚀或其他荷载裂缝的潜在起源点,对混凝土结构的耐久性和安全性构成了严重威胁。
具体来说,振捣时间的长短对混凝土的性能有着至关重要的影响。若振捣时间过短,混凝土中的颗粒无法充分接触和紧密排列,从而导致混凝土的强度不足或不均匀。这种强度上的缺陷,不仅会降低混凝土结构的承载能力,还可能引发裂缝等质量问题。
相反,若振捣时间过长,则会造成混凝土的分层现象。在长时间的振捣作用下,粗骨料往往会沉入底层,而细骨料则留在上层,导致混凝土的强度分布不均匀。此外,长时间的振捣还会增加混凝土的干缩性,使得混凝土在水分蒸发后更容易形成塑性收缩裂缝。这些裂缝的存在,不仅损害了混凝土的美观性,更可能对其结构性能造成不利影响。
7、分段浇筑结合部没有处理好
在混凝土施工过程中,分段浇筑结合部的处理是一个至关重要的环节。当混凝土进行分层或分段浇筑时,若结合部未能得到妥善处理,便很容易在新旧混凝土以及施工缝之间引发裂缝问题,这对混凝土结构的整体性和耐久性构成了严重威胁。
以分层浇筑为例,如果在浇筑过程中因停电、下雨等突发原因,导致后浇混凝土未能在前浇混凝土初凝前及时浇筑,那么层面之间便会产生明显的水平裂缝。这种裂缝不仅损害了混凝土的美观性,更削弱了其结构性能,为建筑物的安全埋下了隐患。
而在采用分段现浇的施工方法时,若先浇混凝土的接触面未能进行充分的凿毛和清洗处理,或者后浇混凝土的养护工作不到位,都会导致混凝土在收缩过程中产生裂缝。这些裂缝可能初期并不明显,但随着时间的推移和外部环境的影响,它们会逐渐扩大,对混凝土结构的安全性和稳定性构成严重威胁。
8、过分抹平压光
在混凝土浇筑完成后,施工过程中的抹平与压光环节虽旨在提升混凝土表面的平整度和观感,但若操作过度,则会引发一系列不良后果。具体而言,过分的抹平与压光会使得混凝土中的细骨料大量上浮至表面,进而形成一层含水量极高的水泥浆层。
这层水泥浆层,由于其高含水量和细腻的质地,成为了混凝土中最为脆弱的环节。当暴露于空气中时,水泥浆层中的氢氧化钙会与空气中的二氧化碳发生化学反应,即碳化反应。这一反应不仅会导致水泥浆层的性质发生变化,还会引发混凝土的显著收缩。随着时间的推移,这种收缩会逐渐累积,并最终以裂缝的形式表现出来,严重影响混凝土结构的完整性和耐久性。
9、养护方法不正确
混凝土的养护环节,作为确保其最终强度和耐久性的关键步骤,其重要性不言而喻。然而,在实际施工过程中,这一环节却往往被忽视或未得到严格执行。许多项目在养护过程中未能严格按照规范要求进行,从而导致了一系列质量问题的出现。
例如,养护过程中不苫盖或浇水不足,无法保证混凝土表面的经常性湿润。这种情况下,混凝土在初期阶段表面失水过快,使得其体积发生急剧收缩,进而引发开裂现象。这种裂缝不仅损害了混凝土的美观性,更可能对其结构性能造成不利影响。
此外,在环境湿度较小、空气干燥、温度高以及风速大的条件下,混凝土的水分蒸发速度会显著加快。这种快速的蒸发过程会进一步加剧混凝土的收缩现象,使得裂缝产生的风险大大增加。
同时,在夏季和冬季这两个季节中,由于昼夜温差较大,若养护不当,很容易产生温差裂缝。这种裂缝是由于混凝土在温度变化过程中受到的热应力作用而产生的,对混凝土结构的稳定性和安全性构成了严重威胁。
10、混凝土早期受冻
在冬季进行施工时,由于气温较低,混凝土面临着受冻的风险。若未能及时采取必要的保温措施,混凝土在早期阶段便可能遭受冻害。受冻的混凝土,其表面往往会出现裂纹,这些裂纹不仅破坏了混凝土的美观性,更可能成为水分和有害物质侵入的通道,加速混凝土的劣化过程。
除了表面裂纹外,受冻的混凝土还可能出现局部剥落的现象。剥落的部分通常是由于混凝土内部的水分在冻结过程中膨胀,导致混凝土结构破坏而产生的。这种剥落现象不仅削弱了混凝土的力学性能,还可能对建筑物的安全性构成威胁。
此外,在脱模后,受冻的混凝土还可能出现空鼓现象。空鼓是由于混凝土与模板之间的粘结力减弱,导致混凝土在脱模时与模板分离而产生的。空鼓现象的存在,不仅影响了混凝土的外观质量,更可能降低其承载能力和耐久性。
因此,在冬季施工时,必须采取有效的保温措施,以确保混凝土不受冻害。
混凝土开裂是一个复杂且多因素的问题,涉及施工过程中的多个环节和细节。为了减少裂缝的产生,确保工程质量,施工人员应严格遵守施工规范,提高质量意识,加强施工现场的管理和监督。同时,还应针对具体工程特点和环境条件,制定合理的施工方案和养护措施,确保混凝土的质量和耐久性。只有这样,才能有效避免混凝土开裂问题的发生,为建筑结构的安全和稳定提供有力保障。
内容来源:砼界张博
免责声明:本文涉及的部分文案、图片、视频摘自于互联网,目的在于分享更多信息,本站不对其准确性负责。部分内容、图片系网络转载,版权归原作者所有,部分内容因转载众多,无法确认原作者,如有问题,请联系删除。