运输机场道面混凝土按其流动性划分干硬性混凝土,其坍落度为0~5mm,在施工过程中大体积浇筑通过振捣的振捣而形成。三轴辊机的压实提浆使其表面形成一层3~5mm左右的砂浆薄层。我们习惯称砂浆薄层的裂纹为龟裂或发丝裂纹,称表面脱层为表面脱皮,严重影响机场道面的使用效果及质量。施工过程中出现面层脱皮龟裂的主要因素如下:
1.原材料中碱集料反应,导致混凝土表层脱皮龟裂。施工过程中,由于原材料中各项化学指标控制不够严格,水泥、碎石、中粗砂、外加剂、水的碱含量超标,每立方混凝土中碱含量超过了3kg/m³。道面施工过程中局部泌水、碱腐使道面混凝土表层脱落,并产生龟裂及松动现象影响道面的正常使用。
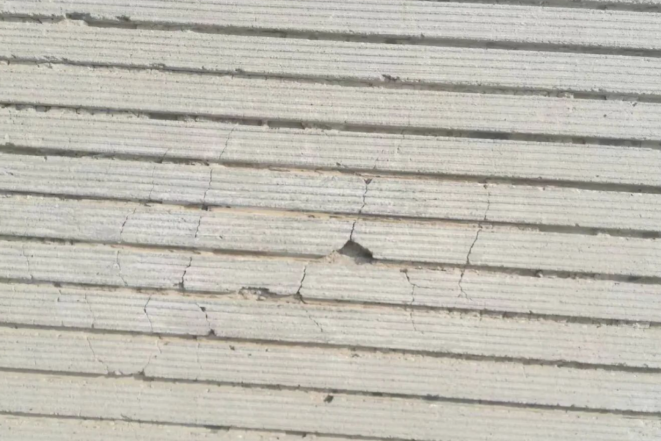
2.混凝土施工工艺是混凝土道面道面表层砂浆与下部混合料存在界面分离,导致面层分离而脱落、龟裂。施工做面时,混凝土已经过初凝状态,洒养生水或水泥浆贴布局部漏石或不平区域,或者抹面过程中污油,其他杂物混入混凝土中,浮于表层,造成界面隔离,容易出现这种龟裂及脱皮现象。

3.养护措施不当,导致脱皮及龟裂。混凝土早期水化热反应十分活跃,混凝土温度可达到60℃~70℃左右。过早喷洒养护水(温度在20℃左右)造成混土急剧收缩,造成表层裂纹。因为温度剪应力造成表层砂浆出现斑状或片状的脱落、龟裂。
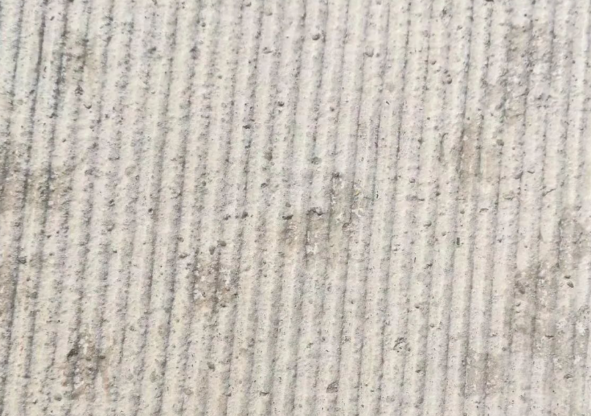
4.由于施工温度以及冻融作用引起脱皮、龟裂。水泥混凝土存在着微观裂隙。当水泥为早强水泥,且工艺控制不严,将导致水泥混凝土的微观裂隙扩大,甚至出现发丝裂纹。积水浸泡,水通过裂缝渗入水泥混凝土中,当气温降至冰点,以下时,水结成冰,体积增大。气温升高时,冰体融化。随着气温在冰点上下变化,冻融过程反复进行,形成冻融循环。冻融损坏是是北方高寒地区造成水泥混凝土表层脱落、裂纹的重要因素。

鉴于上述四条分析,混凝土表层脱皮、龟裂的主要因素应采取以下几点预防对策:水泥:《民用机场飞行区水泥混凝土道面面层施工技术规范》(MH5006-2015)中对运输机场道面水泥混凝土明确规定:“水泥应选用收缩性小、耐磨性强、抗冻性好、含碱量低的水泥”。水泥中的碱含量应按Na2O+0.658K2O计算表示。水泥中的含碱量不得大于0.6%,若同时使用活性材料,每立方混凝土混合料中综合安全含碱量不得大于3kg/m³。水泥应选用旋窑生产的硅酸盐水泥。硅酸盐和普通硅酸盐水泥其强度等级为42.5MPa以上,不宜使用快硬早强R型水泥。水泥的各项指标应符合“水泥技术指标的化学成分和物理指标”:铝酸三钙≤5.0%,铝酸四钙≥15%,氧化镁≤5.0%,三氧化硫≤3.5,28天干缩率≤0.09%,耐磨性≤2.5kg/㎡,游离子氧化钙≤1.0%,混合材的种类不得掺窑灰、煤矸石、火山灰、烧黏土,有抗盐冻要求不得掺石灰岩石粉。运输机场水泥混凝土的上述规定是为了减少面层生产的裂缝以及混凝土强度不能满足使用要求。其次,水泥的细度与水泥混凝土宏观裂纹的出现关系密切。细度越小,强度越高,收缩越大,水化热越大,凝结时间越短。如果水泥细度过细,比表面积大于450㎡/kg时,即使养护到位,混凝土表面仍将出现细微裂缝。道路水泥中规定水泥比表面积在300~450㎡/kg。机场道面混凝土的水泥细度应参照道路水泥标准执行。水泥的正确选用将有效地减轻混凝土道面表面出现裂纹的风险,有助于道面脱皮、发丝裂纹等质量病害防治。碎石(骨料):5~20mm,20~40mm是混凝土用料中的重要材料,也是构成混凝土的骨架,对结构混凝土的工作性能、强度、耐久性起着重要作用。《民用机场水泥混凝土道面面层施工技术规范》(MH5006-2015)中也有明确规定:由于碎石取决于天然石材,受生产工艺及环境的影响,针片状、压碎值、磨耗值、含泥量、碱集料反应均应满足干硬性混凝土的标准要求,级配合理。细集料(砂):采用天然河砂,含泥量不应大于3%、细度模数为2.65~2.85的中粗砂。混合料振捣后,砂中的泥土、轻物质汇聚至表面的砂浆层造成表面强度偏低,受施工气温的影响发育出过多的发丝裂纹,为冻融破坏留下了隐患。因此《民用机场飞行区水泥混凝土道面面层施工技术规范》(MH5006-2015)对砂也作了明确要求,特别是含泥量、细度模数。理论配比要计算,施工控制很关键。施工过程中擅自增加混凝土的单位用水量,使混凝土的水灰比增大,势必造成混凝土中出现大量的自由水挥发,在混凝土内部形成大量的气孔。遇冬季道面积水侵入,容易发生冻融破坏。因此,确保混合料的和易性,准确计算集料中的最佳含水量,杜绝随意增加混凝土的单位用水量,是提高混凝土强度及表层强度的主要措施。搅拌:混凝土混合料的搅拌应注意投料顺序和搅拌时间的控制。民航规范中建议的投料顺序为“砂、水泥、碎石或碎石、水泥、砂”,进料后边搅拌边均匀加水,在搅拌时间的前15秒钟内,将水全部加入搅拌筒(罐)。搅拌时间应根据搅拌机的性能和容量来确定。民航规范要求干硬性混凝土搅拌时间最短时间“双卧轴强制间歇式搅拌机宜不小于60秒”。切实做到:混料生产拌和工厂化,连续工作不间断;投料顺序不能变,搅拌时间经常看,计量准确常计算,拌和时间经常看,维勃稠度勤查验,控制水灰最关键。正确的投料顺序和充足的搅拌时间可以减少混合料中水泥结块,保证水泥在混合料中均匀分布,避免局部结块水泥的过量收缩导致道面混凝土板面表层开裂。另外,若选用水泥的细度较大,要保证混合料中水泥均匀分布并需延长拌和时间。摊铺:混合料摊铺平仓时,应按照配合比确定松铺系数控制松铺高度,杜绝大挖大填,保证混凝土的均匀一致,避免出现局部的砂浆窝。振捣:应采用插入式、平板式、高频排式振捣相结合的振捣方法,严格控制高频振捣器的行走速度,一般控制在0.5~0.8m/s。整平:充分利用滚筒或木行夯的压实揉浆机理,增加混凝土表面3~5mm范围内的密度,有条件的前提下采用三辊轴的整平机进行整平。做面:严格按照“木抹揉浆连续必三遍,铁抹压浆收光再做面,毛刷挺直才能仔细干,表层密实无眼应好看”的工艺标准。充分的抹面可以有力地减少甚至消除混凝土微观裂缝,增加表面密实度,减弱外来水的侵入,提高混凝土面层抗冻性能。做面用三道木抹和三道铁抹来完成。首先第一道木抹将表面揉压平整,压下露石,使泛浆均匀分布在混凝土表层,浆厚达3~5mm;第二道木抹擀出表面泌水,挤出气泡;第三道木抹在5~8m直尺进行压痕检查后继续刮平。第一道铁抹将砂压入混凝土板面,消除砂眼和板面留下的各种不平整痕迹,第二道铁抹收浆,消除抹痕;第三道铁抹为拉毛前最后一道抹面工序,进一步做好压浆收浆工作。做面后表面应平坦、密实、不露砂、无抹痕、无气泡和龟裂。当刮风、干燥、空气湿度小、水分蒸发快,对已拉粗毛的板面要及时采取措施养护,以防表面收缩裂纹。对拉细毛的板面应避免因压抹遍数过多(尤其是钢抹),而产生网状裂纹。养护:混凝土板面拉毛完毕后,应及时覆盖土工布以防混凝土表面收缩裂纹,覆盖六小时以上进行洒水养生,始终保持板面湿润。待强度等级达70%以上方可间断养生,增加粉煤灰活性材料的混凝土可由7天延长至14天,公路工程水泥混凝土道面设计施工规范中已经明示。我们可以得出如下结论:在施工过程中应严格把握支模、配比、振捣、做面、养生各个工艺环节。本文分析了水泥混凝土道面脱皮、裂纹的原因,并提出了相应的对策,为类似工程提供参考。
内容来源:机场技术
免责声明:本文涉及的部分文案、图片、视频摘自于互联网,目的在于分享更多信息,本站不对其准确性负责。部分内容、图片系网络转载,版权归原作者所有,部分内容因转载众多,无法确认原作者,如有问题,请联系删除。